PT Ain’t What It Used to Be
Newer pressure treatments don't offer the same rot and decay resistance. Follow these simple strategies to give outdoor lumber its best chance of survival.
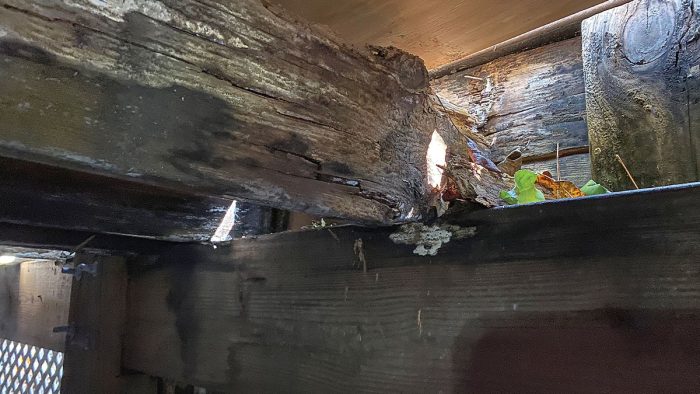
Changes in the chemical formulations of pressure-treated lumber beginning in 2004 have yielded lumber that is not as rot-resistant as it used to be. Doug Horgan’s company has responded by making changes to some standard practices: using only ground-contact PT lumber, flashing the tops of joists and beams, treating field cuts, keeping lumber away from grade, and creating spaces for drainage and drying.
Time for Change
Until a few years ago, pressure-treated structures were pretty forgiving. We buried fence posts in the dirt. Treating cuts with brush-on preservative wasn’t required, and there weren’t any flashings, coatings, or tapes covering the tops of joists and beams. There never seemed to be problems.
When our go-to CCA (chromated copper arsenate–treated) southern yellow pine was taken off the residential market in 2004 because of toxicity concerns, we had some reservations about the new treatments, but things seemed fine for years—until we had a handful of shocking treated-wood failures. These failures revealed that we’d have to change our construction methods if we wanted this new outdoor lumber to last as long as the old stuff.
Signs of Failure
One of the first indications that the newer treatments weren’t like the old was a call we received in 2020 about a deck we had built in 2013 that the client said felt springy and soft in areas. It was a pretty standard backyard deck, about 4 ft. above the ground with plastic cap-stock decking.
What I found when I crawled underneath was far from ordinary. Mushrooms were growing out of the joists, and black and white fungi covered their sides. There were a few places where the joists had crumbled, as well as many smaller areas of damage where water had gone between the deck boards. In total, we found 70 damaged joists, beams, and posts on this deck.
A couple of years later, we had another surprise when past clients told us there was something unusual about the hot-tub platform we had built for them in 2013. When we checked it out, we found one of its 2×12 main beams had a visible sag, areas black with rot, and white fungus all over. Surprisingly, the damaged area was in the middle of the beam, not at the cut ends, and the attached joists had no decay despite the end grain being in contact with the rotting beam.
There were other failures, too, including tongue-and-groove decking that a client’s foot went through, and a treated glulam with enough rot to develop an obvious sag.
Warranties Are Inadequate
Given the seriousness of the decay, we fixed these problems even when the projects were no longer under our warranty. The damage varied from a substantial rebuild, including replacing some railing sections, to much simpler replacements of individual pieces, like the hot-tub beam and rotted tongue-and-groove decking. We attempted to use the warranty coverage provided by the lumber-treatment company in at least one case, but the coverage was disheartening.
Even if we were able to meet the warranty requirements by providing the purchase receipt and submitting photos and sections of damaged wood, the warranty would only cover replacement pieces provided at the company’s loading dock, or a refund of the original purchase price—the company’s choice.
There would be no reimbursement for our time spent working with the clients and filing a claim, taking apart the structure, disposing of material, and doing the reconstruction, or for other materials like hangers, fasteners, or decking and railings that didn’t survive disassembly. Our lumberyard got some additional costs covered on one project, but even then these were expensive repairs.
Given the costs and hassle of dealing with PT failures, we’ve since made some changes to our standard practices, including flashing the tops of joists and beams, treating field cuts, keeping lumber away from grade, and creating spaces for drainage and drying. So far our improvements seem to be working, but only time will tell.
Lessons for Longer-Lasting Lumber
There are a number of ways we’ve learned to give modern pressure-treated lumber its best chance of success. We use lumber with the appropriate ground-contact rating, and we prevent debris and water from getting between multi-ply beams and into joist interiors. Also, we try to prevent dirt and organic material from accumulating around posts and framing, and we leave a drainage space between trim and frame components.
Treat Field Cuts and HolesField treatment is required by the International Residential Code (section R317.1.1) and is also a warranty requirement, but when we started looking for copper naphthenate or similar treatment solutions, we couldn’t find them at any local suppliers. At our request, a local yard now stocks a field treatment we can add to the lumber delivery. It’s messy and the directions make it seem like hazardous waste, but we’ve seen the disastrous results of not using it. |
![]() |
Use Only Ground-Contact PT
The American Wood Protection Association (AWPA) classifies PT lumber into categories that describe the type and level of exposure a wood product can safely withstand, based on its treatment with preservatives. These categories help guide users in selecting the appropriate wood for various applications, such as above-ground, ground-contact, or underwater. In 2016, the AWPA changed the guidelines of where ground-contact-rated PT lumber (UC4A) should be used to include structural members, places where leaf debris is expected to build up, or wood within 6 in. of the ground. Our main lumberyard announced in 2016 that it would no longer sell treated wood that wasn’t ground-contact rated.
![]() |
![]() |
Tape Joist TopsThe tops of deck joists are riddled with hundreds of holes from the deck-board screws. Water from rain, snow, and washing follows the screws into the joist center, where it can’t dry and where there’s often less chemical treatment. To seal around screws, we use a flexible UV-resistant flashing tape designed for this purpose. The 1-5⁄8-in.-wide tape we use from Trex sells for $0.50 per ft. |
![]() |
![]() |
Cover Multi-Ply BeamsWhen rain and debris get between the layers of built-up beams, the perpetually wet and dark conditions create the perfect environment for decay-causing microbes and fungi, so we cover their tops with flashing tape. Our local yard stocks a 3-1⁄8-in.-wide roll from Trex that costs about $1 per ft. |
Keep PT Above Ground
We keep footings for posts, stairs, and decks above grade and use metal connectors for attachment. We also keep decorative wraps above ground level to keep insects from using them to reach the lumber posts and frame above. For freestanding structures we now use Simpson Strong-Tie Moment Post Bases, which keep the wood posts out of the concrete and resist racking.
![]() |
![]() |
Leave Space Behind Trim
Band joists, stair stringers, and beams are often covered with PVC, poly-ash, and other synthetic trim. To prevent water from becoming trapped behind the trim, we space the trim away from the PT frame. I prefer 3⁄8-in.-thick spacers, which eliminates having to mortise the trim over the bolt heads, saving time. We space them whatever the trim manufacturer recommends for on-center spacing and fasten the trim through the spacers. We also follow the trim manufacturer’s recommendation for butting or mitering corners.
![]() |
— Doug Horgan, VP of best practices for BOWA in McLean, Va. Photos by the author, except where noted.
RELATED STORIES
- What’s the Difference: Pressure-Treated Lumber
- Pressure-Treated Lumber Worries
- Staining Pressure-Treated Porch Posts
Fine Homebuilding Recommended Products
Metal Connector Nailer
MicroFoam Nitrile Coated Work Gloves
N95 Respirator
View Comments
What product did you use to treat cuts and holes?
Harry
Louisville, KY