Talking Shop
A custom finish carpenter shares how he designed and outfit his two-car garage shop with all the tools, jigs, and accessories he needs to comfortably do great work.
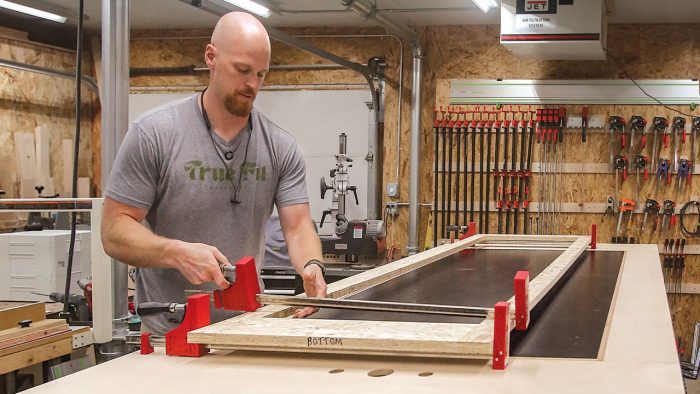
Finish carpenter Casey Knips built himself a workshop in his home’s 24-ft. by 25-ft. garage. He began the shop organization process
by creating a digital model of his ideal shop. This then allowed him to move his tools and materials into place immediately rather than figuring out their placement through trial and error.
This shop has all the essential tools and machines for Knips’s carpentry work, adequate storage space for lumber and clamps, and a dust collection system that includes an articulating boom arm. Knips believes that having powerful stationary tools; a big, comfortable work surface; a full supply of clamps; and the ability to easily keep his workplace clean is better than even the best job-site setup.
A Good Shop Can Make a Big Difference
Some of a carpenter’s genius is figuring out how to use off-the-shelf materials, tools from the truck, and clever jigs to get great results on custom projects done entirely on the job site. And on some of my projects, I work that way. But I also value having a dedicated shop—and whenever I can, I use it.
I find having powerful stationary tools; a big, comfortable work surface; all the clamps I need; and the ability to effortlessly keep my workplace clean has more potential that even the best job-site setup. For example, with a jointer and planer, I can mill lumber of any species my client wants to any dimensions the project calls for; with my router table or shaper I can safely make custom trim profiles in a wide range of sizes. Working in my shop, I have more control, and therefore, I tend to get better results.
Woodshed the PlanCreating a digital model of my desired shop was time well spent. Not only was I able to take a trial-and-error approach to tool placement, but I worked through workflow, clearances, and storage areas before I loaded the garage with tools and materials and made it more difficult to rearrange. For example, by the time I moved my tablesaw to its place in the shop, I knew exactly how much space I would have on both the infeed and outfeed sides. My model was helpful when it came time to have dust collection and lighting designs done too. |
Size, and Tools, Matter
This doesn’t mean that a finish carpenter like me needs a particularly big or expensive shop. My shop is on the property where I live. It’s a slightly oversized two-car garage at 24 ft. by 25 ft. I do custom finish carpentry, which includes adding trim details like coffered ceilings and wainscot paneling, building and installing big doors, and some cabinetry work. I generally work alone, and this size shop fits all the tools I need.
There’s room for infeed and outfeed on both sides of tools through which I might be running long materials, and just enough room for material storage, though I don’t have the luxury of stockpiling materials that I may use in the future. If I’m not pretty certain I can use a particular board or partial sheet good on a coming project, it has to go so there is space for the necessary material for my next project.
As you see, I do have a lot of expensive tools and machines, and I admit to being a tool junkie, but I buy them as jobs arise where they’ll make the work better, faster, or safer to do. Most of the tools you’ll find in my garage are expected in a woodshop, and I’ll focus on the most common and what I consider shop must-haves in this article, but I do have some luxuries too. For example, I have both a router table and a shaper.
Workshop EssentialsEvery carpenter will have different requirements for organizing a shop based on their work and their preferences. I can’t imagine too many carpenters who don’t need an easy-to-use and dedicated miter-saw station and worktable, though. It’s also important to consider power, heating and cooling needs, and safety in your shop.
![]()
|
A shaper does similar work to the router table but can handle a bit larger material and larger profiles, and I can have custom cutters made to match profiles that my clients already have. My 3-hp Delta shaper is probably 30 years old, and though I may upgrade to a bigger machine at some point, it still works great. It is also set up with a power feeder from Co-Matic.
Even though I don’t use my Powermatic drill press as much as I thought I would, when it comes time to make large-diameter and repetitive holes, sometimes at an angle, I’m glad to have it. It recently paid for itself on a complex stair-rail project.
Similarly, my Powermatic bandsaw is powerful and has great cut capacity, and its table is set at a very comfortable height for me. I do a fair number of projects with shop-sawn veneers, so this tool is a must-have. The bandsaw is tucked farther away than most of my other tools, but all I have to do is move a couple things out of the way and I can push boards up to 9 ft. long through the bandsaw.
I also have a drum sander and a dedicated sharpening machine. I don’t use them too often—I should definitely sharpen more— but when the time comes to roll either of them out, they do better work faster than I could do with alternative tools.
Not-So-Stationary MachinesOne of the main reasons for a finish carpenter to have a shop is to access tools that are less common on job sites but that improve the quality and safety of the work. For example, a powerful planer makes it easy to mill boards to custom finished dimension; a router table is more precise and safer than a handheld router. These “stationary” machines are big and heavy, which is why they’re not common on job sites—but I’ve put them on mobile bases so I can move them around.
![]()
|
OSB Walls, Because It’s a Shop
When it came time to convert this garage into a shop, I had a lot of decisions to make, from how to insulate the walls and ceiling and how to finish the walls, to where to put the tablesaw and where to store my many clamps. One good decision I made in regards to shop organization was to finish the walls with OSB.
It was fast (just screw it to the studs; no taping), it’s durable, and I can fasten a shelf bracket, a hook, or an accessory to it anywhere I want. I have very simple and very convenient sawblade storage in the back corner of the shop that is no more than a screw partially driven into the OSB.
The ceiling I did finish with drywall. At 8 ft. 6 in., the ceiling is a little low sometimes. I did have to bump up the area above the dust collector, which is quite tall. With light fixtures and dust-collection piping, it can be a bit tight when moving sheet goods and other long materials around in the shop. Still, raising the ceiling was a cost and complexity I decided against, and I don’t regret it yet.
While the biggest storage challenge in a small shop is finding places for lumber, tools, and accessories, and I’ll get into how I solved some specific challenges—like where to put my clamps—in more detail, every shop needs some kind of catch-all space for random items.
I took care of some of this with a kitchen’s worth of secondhand cabinets. I used the base cabinets in a few locations, including for my miter-saw station, and the wall cabinets in a couple other locations for more general storage. This was an affordable approach, and one nice thing about the upper cabinets is that they keep the floor space below open. That said, as I get more specific with storage solutions, some of the uppers may get replaced with dedicated storage.
Storage SolutionsThe right workshop storage makes the difference between an organized and convenient shop and a messy one. My storage setup is ever-evolving, but worth all of the time and money I have put into it. ![]() ![]()
|
Design Tool to the Rescue
I could have loaded my worktable and all my tools into the shop, taken a guess at where everything should go, and then rearranged as I learned about how I used the space. But these tools are heavy, and my worktable is nearly immobile—plus, I may never have come to some of the helpful decisions I made in the planning phase if I had taken that more haphazard approach. Instead, I used an online tool to plan the shop layout, and it was helpful in some surprising ways.
After drawing out the shop footprint, I started to place the tools I had, and the tools I planned to buy in the near future, into the digital model. I tried out various layouts that gave me the most infeed and outfeed where I needed it and made sure there was enough room to move materials around between workstations.
For example, I positioned the tablesaw with 10 ft. 6 in. on the infeed side and 10 ft. on the outfeed side. Most of the time, that’s more than enough space, but I positioned the saw so that if I need just a little more room, I can open the garage door and move the saw just a bit toward it.
Dust-Collection DetailsDust collection keeps the shop clean and me healthy. Remember, sawdust is a carcinogen. I use a combination of a central dust collector, a shop vac, and an air filter, as well as a few accessories to keep the air clear and the shop clean. ![]() ![]() ![]()
|
I also realized during this exercise that I didn’t need two operational garage doors. One would be plenty for bringing tools and materials in and out of the shop. Closing the second door off not only makes the shop more comfortable (garage doors are basically thermal holes in a building), but it gives me another big wall space for tool storage.
Finally, the model helped me determine where I needed things like electrical outlets and dust collection. In fact, the companies from which I purchased the dust-collection piping and the lighting used my digital model to design layouts and choose products for the shop. Both systems are working really well.
Like I mentioned earlier, I’ve innovated a lot of on-site solutions to building challenges. But if I have to build custom doors, run miles of molding through a router, or assemble an office’s worth of built-in boxes, I’ll take a shop any day. And this two-car garage is just enough. It’s tight in here, but it works.
— Casey Knips; operator of True Fit Carpentry, a custom trim and cabinetry company in the Twin Cities. Photos by Brian Pontolilo.
RELATED STORIES